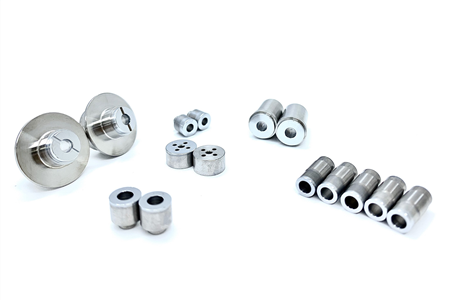
The method of surface treatment of metal plating
- Mechanical grinding method: Use grinding powder (aluminum oxide) and grinding tools to conduct rough grinding, fine grinding, ...
- Method of spinning ball: Including dry ball and wet ball spinning, applied with small details, can not be ground.
- Chemical method: Remove grease, remove rust stains to avoid coating stains and peeling. This method includes degreasing in organic solvents, degreasing in emulsions and lye, degreasing by electrochemical methods, etc.
The metal surface treatment chemicals
- Water or powder alkaline pickling: Applicable to base metals such as copper, zinc, iron, steel, aluminum, metal plating ... This chemical is strong, medium or mild alkaline, depending on the needs. Use accordingly.
- Water acid degreasing: Use to remove grease from the base metal by immersion at room temperature for about 20-30 minutes. In particular, this solution is capable of degreasing on galvanized steel materials without affecting the zinc layer.
- Aluminum degreasing: Greasing effect, simultaneously regenerating the surface for aluminum metal materials.
- Zinc phosphate: Create a zinc phosphate layer on the metal surface and this zinc phosphate layer is stable in air environment, has good resistance to rust and corrosion, and increases the grip and elasticity of the layer. plating. Zinc phosphate is mainly used in powder coating.
- Forming agent: Has the effect of shaping and neutralizing the metal surface, at the same time, it promotes the phosphate process faster, and the phosphate layer is covered evenly, finer, more adherent on the surface of the metal material. .
- Catalyst, accelerated: Helps shorten the time of phosphate process.
- Chromium: Is a common plating industry, capable of passively dyeing chromium for zinc and cadmium plating layers, making these plating shiny and colorful, especially resistant to eating. Very high wear.
- Sulfuric acid: Transparent, colorless, soluble in water, used to remove rust during surface treatment